Printed circuit boards (PCBs) are considered core ingredients of contemporary electronic devices and modern technology. Fabrication of PCBs has a critical role in the production of electronic devices in all industries such as automotive, consumer electronics, and cellular technology. The procedure of printed circuit board fabrication is very complex and maintains the critical link between design and the physical electronics world. Almost all of the electronic devices are merged over the PCB’s surface through passing complicated stages and result in unified functional devices. The printed circuit boards are manufactured from different types of PCB materials and each material has its pros and cons. PCB material types depend on the application for which the PCB is being fabricated. This article deals with the types of PCB materials in detail.
Basic Construction of Printed Circuit Board
The flexible and rigid PCB material types are chosen based on environmental and electrical properties for optimum operation after the PCB is fabricated. The schematics of the printed circuit board dictate the layer numbers and the board’s form factor. Traditionally, the supplier of the board delivers stackup of materials that are selected based on PCB design. The following are some key points to be considered for the selection of PCB board material types.
1. Copper Traces
Copper is a very high conductive element which is utilized for making the traces that are on the circuit board for conduction. It provides the pathways for electric current to flow through the board. It is an important electronic component in PCB material types.
2. Silkscreen
Silkscreen is printed onto the PCB board digitally and has no impact on the PCB functionality. Silkscreen assists in the recognition of different components and warning symbols. It also helps in the identification of different test points and marks of manufacturing. Silkscreen layer is typically printed in white or black ink and is placed on top of the copper traces and other layers that make up the PCB board.
3. Solder Mask
Solder mask is a method in which the circuit board’s every part is having a coat of epoxy layer with the exception of contacts that are to be soldered.
Understanding the PCB Core Material Types
The following are some important terms that are to be understood by designers before designing and fabricating printed circuit boards and must also have a grip on understanding the PCB core material types.
1. Annular Ring
An annular ring is surrounding the holes onto the printed circuit board that are typically of copper metal in which component pins are placed. Annular ring is one of PCB core material types in PCB manufacturing.
2. The Design Rule Check
Design Rule Check is also known as DRC and is a technique for double checking the process of the printed circuit board for checking any sort of errors present in the circuit board.
3. Buried and Blind Vias
This is a technique for checking the layer-layer connection within the printed circuit board. Furthermore, the process is also utilized for trace routing in the vertical direction within the board from one of the layers to another layer without having any plated through holes.
4. Traces
Traces are the layers of copper metal for signaling within the circuit board or it can be stated that these are responsible for the conduction of current within the circuit board. Traces are often known as wires but these are not wires. However, the purpose is the same except that traces are not laminated.
5. Surface Mount Technology
Surface mount technology is the process of placing components onto the printed circuit board through automatic equipment. The components are soldered in an oven which has a conveyorized reflow mechanism.
Materials Utilized for Printed Circuit Boards Manufacturing
PCB material types selection and its integration within the circuit board is of critical importance in the process of PCB manufacturing. There are thousands of different types of PCB materials that may be utilized for the fabrication process but these types of PCB materials are chosen based on different factors such as efficiency, cost, and technical properties. The following are some most widely used PCB board material types throughout the world.
1. FR-4 Material
FR-4 is a material that is being graded by the National Electric Manufacturers Association and is one of the flame-resistant materials consisting of a layer of woven-glass fabric as well as an epoxy resin binder. This material has been utilized for PCB manufacturing for over 50 years now and has been in constant evolution. The PCBs manufactured from FR-4 material work in high temperatures of over 180 degrees Celsius. However, the material is not considered best if certain properties like the coefficient of thermal expansion are considered. This material is also not good for applications in which high-speed signals are to be managed. This is the reason why this material is now less utilized for PCB fabrication. FR-4 is the one of the most commonly use PCB board material types.
2. Teflon
Teflon material is utilized in the fabrication of printed circuit boards recommended for applications such as radar and high-speed communication, for instance, satellite dishes. Teflon is considered better than FR-4 and other resin materials in PCB material types.
3. Roger Material
This type of material is recommended to be utilized in digital product applications where the requirement for higher speed of signals and its integrity is expected. The manufactured PCBs are expected to withstand high temperature. Such materials are not included in either Teflon or FR-4 materials but are categorized independently in PCB board material types.
4. Polyimide
This is among the top-performing PCB material types. It has fantastic mechanical, thermal, and chemical properties. This material is most widely adapted to applications in which there is a requirement for higher reliability, resistivity, flexibility, and temperature resistivity. This is a thermosetting polymer offering exceptional dimensional capabilities and shows great resistance to various chemicals affecting the performance of printed circuit boards. This material has higher thermal stability, has flexible nature, and perfect chemical resistance. However, it has a few disadvantages too such as high expense and challenges while processing it. Polyimide is one advanced PCB board material type.
5. Epoxy Composites
The epoxy composites are also known as CEM-3 which is very similar to FR-4 material when its composition and performance are considered. This material is composed of woven glass fiber along with resin epoxy. The material offers high electric insulation, thermal stability, and mechanical strength compare with other PCB material types. Some of the key advantages of this material are good performance and cost-effectiveness. While its disadvantages comprise low thermal stability and limited performance in higher-frequency ranges.
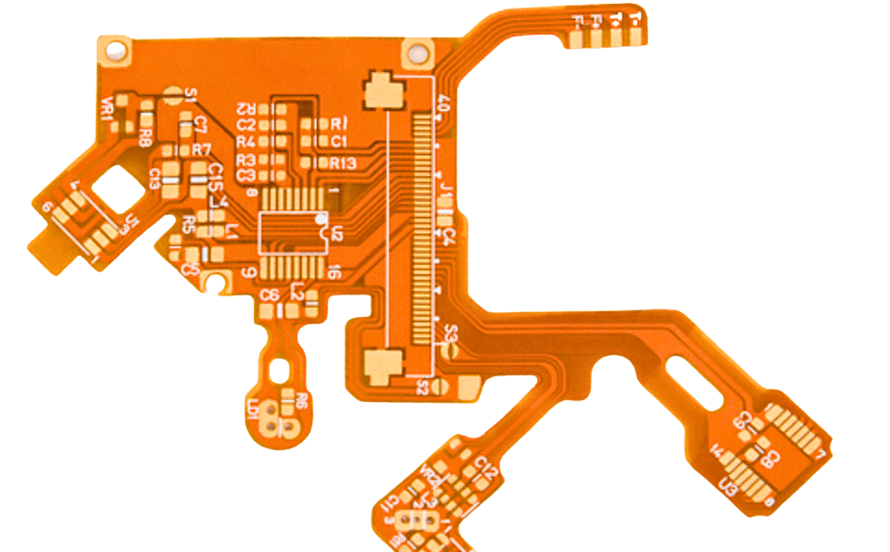
Considerations for Selection of PCB Core Material Types
The following are the main considerations to be adhered for the selection of PCB material types.
1. Purpose of the Circuit Board
The purpose or application for which the PCB is intended to be designed must be clear. Therefore, it is highly recommended that a prototype is to be made considering all of the requirements of the board. All of the properties such as signal integrity, thermal resistance, temperature resistance, and attributed environmental factors must also be considered in the selection of PCB material types.
2. Electrical and Non-Electrical Properties
Electrical and non-electrical properties such as power thresholds, conductivity, transfer of heat, and other properties should be kept in mind so that the material is capable of delivering good results when PCB is manufactured. For example, in today’s era overheating is a big concern in mobile phones, biomedical devices, wearable gadgets, and laptops. Therefore, the selection of material must be efficient enough to bear high temperature and have good electrical and non-electrical properties.
3. Stack-Up
Stack-up always plays a crucial role in the design of PCB with aspect to a mechanical engineer. Stack-up is for fitting the printed circuit board into the device. The stack-up may be of single or multiple layers. This part of the design process also referring to impedance requirements.
4. Mechanical Properties
Checking the mechanical strength of the types of PCB materials to be utilized for fabrication is of great importance. The material must be strong enough to resist harsh environmental conditions.
5. Location of Components
The signal integrity may be at stake if signals are flowing through different components that are generating constant noise which is also known as interference. Therefore, the location of components must be ideal all through the circuit board and must be verified in the stage of the design.
6. Cost
The PCB board material cost is also a key factor influencing the design of the circuit board. Therefore, the selection of PCB material types must be made so that the cost is not beyond a certain threshold. This is for making the PCB to be manufactured affordable and cheap. Other factors may also increase the price of PCB fabrication such as taking the spacing less than 6 mils.
Conclusion
The selection of the right kind of PCB material types is of great importance as it shapes the electric design of the circuit board. Furthermore, the chosen material is also influencing the performance of the circuit board along with other factors such as cost and reliability. With understanding of various kinds of PCB material types from which PCBs are manufactured, considering a few parameters are of critical importance such as environmental considerations, resistance to different chemicals, mechanical strength, and thermal and electrical performance. With the constant advancement in technology, the advent of new types of PCB materials is also expected which will bring their pros and cons to the PCB fabrication industry.