The world of silicone rubber molding takes you into a realm where innovation and accuracy come together and coexist. New tactics that include nothing less than the best mold design and faultless process control are some of the strategies that make us the best.
The use of these techniques not only results in enhancing production efficiency but also the quality of products, especially in those industries with high expectations of the output in terms of performance and reliability. Adapt these tactics to convert adversities into victories in molding silicone.
Definition of Silicone Rubber Molding!
Silicone rubber molding is a detailed method for making silicone, which is hard-wearing and can be stretched into shape. This process consists of heating the silicon material and then injecting it under high pressure into a mold that has been previously designed and customized. Once cured, the silicone will capture the mold’s intricate shapes giving parts a high degree of accuracy and detail.
Perfected for medical, and automotive industries as well as consumer goods, this method is versatile in that it possesses properties that enable it to be heat resistant, chemically stable, and biocompatible.
Advanced Mold Design Techniques!
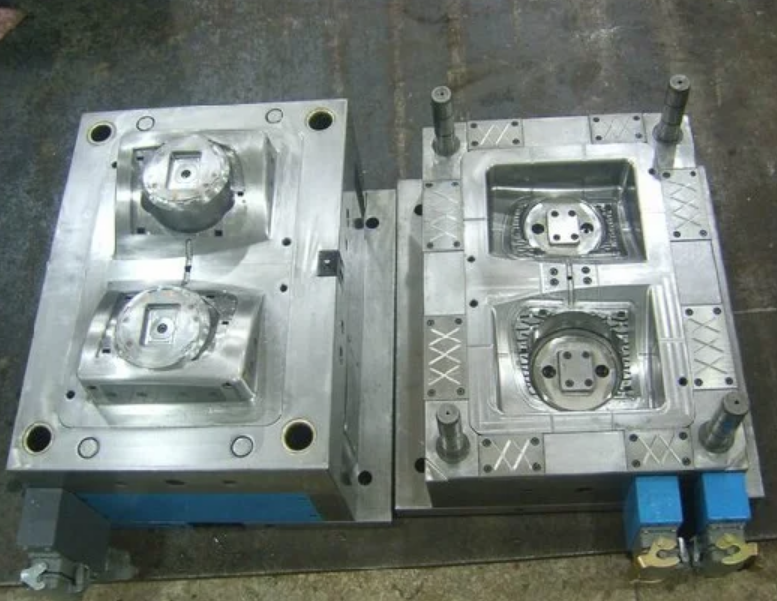
● Incorporating Advanced Features for Complex Shapes and Designs
⮚ Incorporating Multi-Cavity Molds
Adoption of the multi-cavity molds by silicone rubber molding technique aims at increasing production efficiency by manufacturing several parts concurrently.
Such an intricate design technique is not only capable of scaling up the output; it also guarantees uniformity among each component. Suitable for deeply weighted demands, the multiple-cavity molds bring out resource optimization in their way, a critical feature of streamlined manufacturing metal fabrication processes.
⮚ Implementing Core-Pulling Mechanisms
Through the core-pulling mechanisms, mold making of silicone materials is revolutionized in the sense that a material can now produce complex and intricate designs that were earlier complicated.
It is a novelty that allows forming overhanging and recessed parts without lowering the mold integrity, thus, increasing the number of types that can be produced. These techniques reinvent mold agriculture, making the process even more viable and preparing the grounds for more advanced product designs.
⮚ Introducing Advanced Cooling Channels
A significant decrease in cooling channels of the molds in silicone rubber results in reduced cycle times due to improved heat dissipation.
These channels are always to be located tactically, solving the problem of cooling uniformity, reduction of the warpage, and shrinkage. It would bring about a quicker molding of the parts with the quality; a considerable leap in mold efficiency and product consistency would be observed as well.
⮚ By leveraging the Molding Flow Analysis Program
Innovative mold flow analysis software in the rubber molding of silicone allows one to analyze the process of injection and get a completely new insight.
This technology enables to forecasting of understudied flaws; therefore, preliminary corrections can be implemented. It accomplishes this goal through mold and process design optimization, which ensures optimal material flow and cooling, without which could be impossible to do flawless parts.
● Utilizing 3D Printing Technology for Prototype Mold Development
⮚ Rapid Prototyping
The quick prototyping makes silicone rubber molding faster because it enables a timely mold creation, which in turn, makes design validation possible at once.
This mission, which is difficult to achieve because of LSR molding service, shortens product development cycles and provides real-time feedback; the latter can be implemented immediately and corrections to be done. It manifests the concept of efficiency through the reduction of the concept to the final product time frame, and it also accentuates the agility of adaptation to market trends.
⮚ High-Resolution Printing
3D printing composite materials with a high resolution are revolutionizing silicone rubber molding as they allow the production of models with the ultimate level of detail and accuracy.
This technology is perfect for producing such complex geometries that traditional methods cannot, and as a result, the most accurate reproduction of the most detailed designs is achieved. It elevates the quality of silicone molded parts to a level that is sometimes even beyond the required standards in varying applications.
⮚ Integration with CAD Software
This is a significant achievement in the history of molding and involves combining 3D printing with CAD software. This integration enables the smooth transfer of digital designs into real molds that in turn enhance the design process.
Engineers can iterate designs very fast which ensures that the final molds are precisely along the specification. This integration helps to standardize the workflows and ignites innovation in the silicone molding industry.
Optimizing Process Parameters for Enhanced!
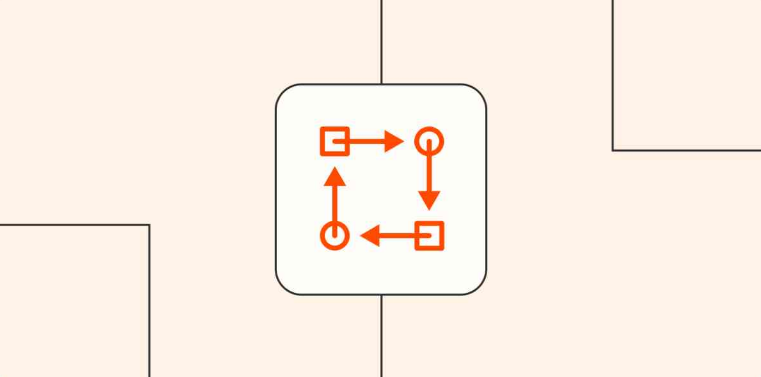
● Temperature Control
Temperature accuracy becomes the key factor in the molding process of silicone rubber since it ensures the material goes to the mold smoothly. Sufficient heat temperature ensures no heat burns or under fills which is a must for a perfect part formulation.
Temperature control is an essential aspect and proficiency in its parameters prolongs the life of molds, which increases the stability of the quality of parts, thereby establishing a good manufacturing foundation for perfection.
● Pressure Adjustment
It is an art to control the pressure in silicone rubber molding, the balance of power between the mold and the molding object without fault. Correct pressure makes sure that silicone gets between all the small spaces, capturing all details. The closed loop tool adjusts pneumatics to avoid air entrapment in addition to flashing which is of the uttermost importance for making parts of high specifications.
● Injection Speed
Injection rate is a considerable factor that controls the flow of the types of materials and mold filling in the making of molds using silicone rubber molding. The accurate calibration will provide fast and uniform filling, leading to an elimination of air pockets and improvement in the material quality. Improving speed ensures a high level of cycle efficiency and part integrity, especially in the case of high-volume runs.
● Curing Time
Time cure is critical in molding in silicone rubber which affects the elasticity and strength of the parts molded. Good timing is important to ensure a complete cross-linking process which is critical to the material’s performance properties.
Surface Finish Enhancement Strategies!
● Implementing Mirror Polishing Techniques
The mirror polish techniques for silicone rubber molding, make the molding surface finish look more attractive than before. Through the rigorous process of cold working, we obtain shiny, even-looking parts that look good and are functional at the same time.
This approach is very effective for consumer products, but in terms of visual appeal and cleanliness, it also meets high standards of hygiene that are very important in applications where there is a need for cleanliness.
● Utilizing Chemical Etching
Chemical etching becomes a way of adding fine details and textures to molded silicone rubber parts, achieving both matte and complex prints. Because of this through the creation of coatings, properties like grip and tactility are controlled and can be customized to specific needs.
One of the features of this technique is that it enriches different existing items, from healthcare instruments to automotive parts, and many others in between.
● Introducing Surface Coatings
Specific coatings on the surface of silicone rubber castings give added shielding and performance enhancement. The coatings can further be etc, anti-microbial layers to UV-resistant films and such, extend the lifespan of products and broaden their application scope.
Using appropriate coatings manufacturers can satisfy different industrial standards, so their end products will be resistant and efficient during usage in extreme conditions.
● Incorporating Laser Engraving
Laser marking in silicone rubber molding is the technology that enables accurate branding or features with high-precision machining and detail on the parts. Using this method is a technique for a liquid silicone rubber molding service that can see the addition of logos, serial numbers, or instructions that are clean and permanent. It could be used to provide function and a brand for an individual product molded to order.
Importance of Quality Control in Silicone Rubber Molding!
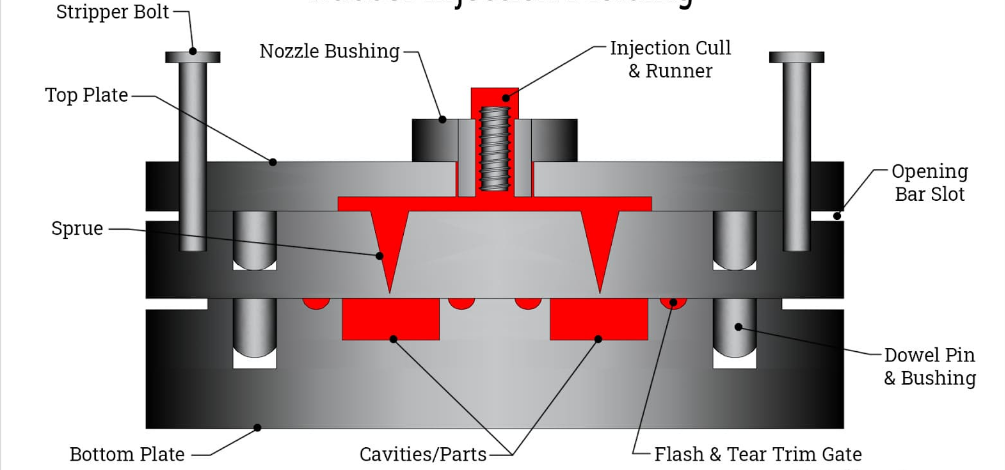
● Coordinate Measuring Machines (CMM)
The Coordinate Measuring Machine (CMM) is a crucial tool in silicone rubber molding as it is crucial in ensuring that the parts that are produced meet the strict dimensional specifications.
With this precision tool, one can draw up the geometry of finished parts even in the case that the deviations are minute compared to the design. This usage underlines a drive for excellence which is vital for application areas that demand very high accuracy for instance in medicine and aviation.
● Non-Destructive Testing Methods
Non-Destructive Testing (NDT) methods make sure that silicone rubber parts are safe, without causing damage to the parts while testing. Functionalities like ultrasonic testing and X-ray imaging help to find internal flaws during inspection, thereby ensuring reliability without compromising the usefulness of the part in question.
This strategy is vitally important for the achievement of the main objective – the maintenance of the required quality and the function of key components.
● Statistical Process Control (SPC)
The quality assurance approach for silicone rubber molding using SPC as a data-driven approach is what Statistical Process Control (SPC) offers. Through monitoring and analyzing process variables, manufacturers can find ways to eradicate dynamics problems by altering and correcting the defects in real-time, hence, improving consistency.
Conclusion
Success in silicone rubber molding requires more than just regular Knowledge; it requires special skills that are aimed at providing accuracy, toughness, and efficiency. Performing these procedures can highly increase the level of quality and performance of these products contributing to the widespread use of molded parts across many applications. For those who are serious about their silicone rubber molding projects, visit 3ERP, which is the home of the latest technological development and increased knowledge in the sector.